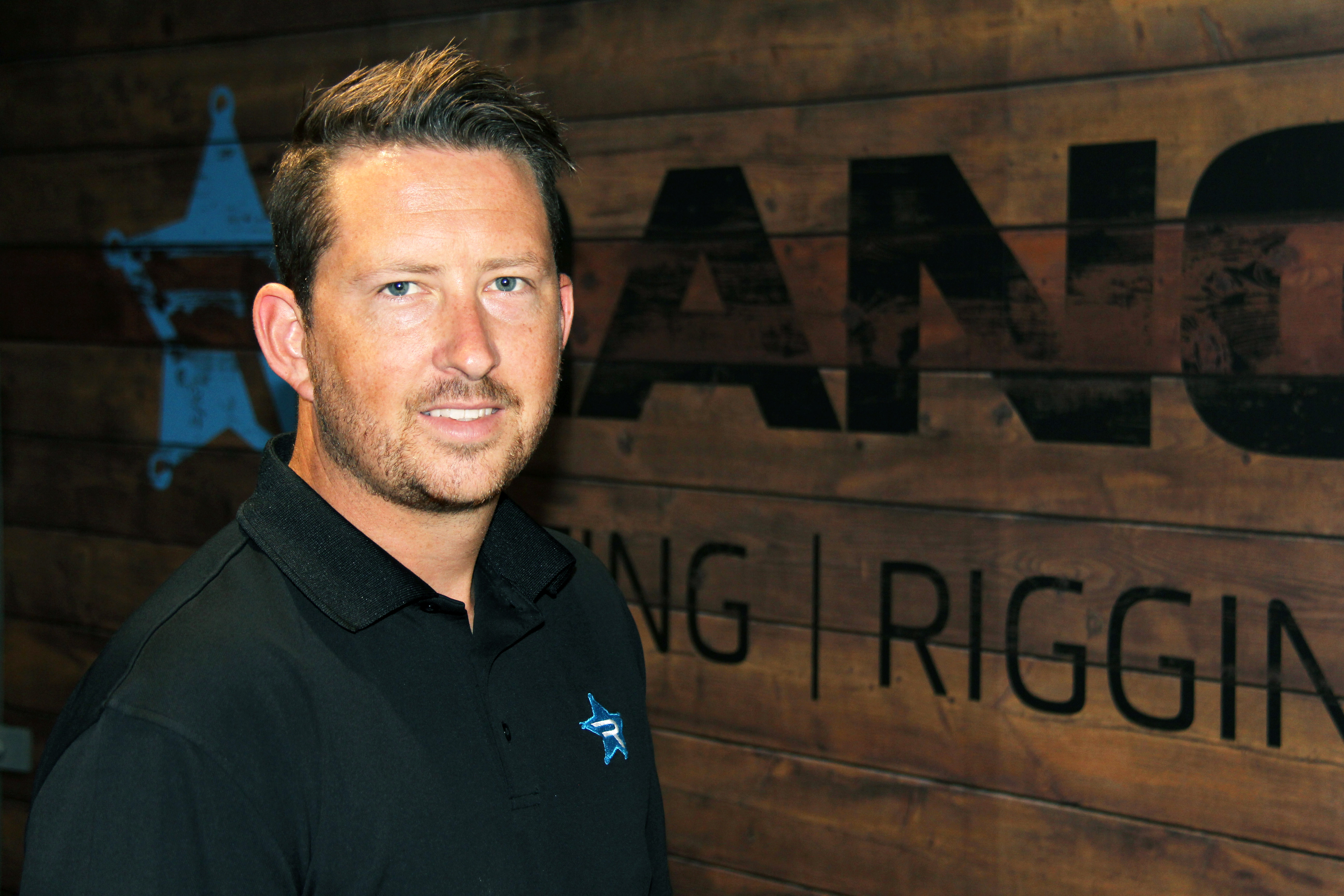)
Shock Loading
Rigging gear is particularly vulnerable in the event of shock loading.
To begin to understand shock loading, we need to accept the definitions of ‘shock’ (a sudden or surprising event or occurrence) and ‘loading’ (the application of a load or force). Put the two together and we’ve got a scenario where a crane, hoist and / or rigging gear is ‘shocked’ by a load or force greater than which it was designed to withstand.
As we will explore, it’s important to understand ‘dynamics’ too, whereby a period of—or constant—change is applied to a situation (or lift).
I get quizzed a lot about shock loading, and two realities hit me with the force of a dropped load:
- People overlook the fact that lifting gear can be overloaded and damaged even though the weight being lifted is less than the working load limit (WLL) of the crane, hoist or rigging item.
- They look in isolation at the crane or hoist as the thing that feels the full force of a shock loading incident. In reality, the rigging gear (the equipment connecting the load to the crane) is often much less well equipped to survive such force and is exposed as a link in a chain of lifting equipment.
When does shock loading happen?
You might only ever be a moment away from a shock loading incident, particularly if competency and training are lacking at any stage of the process related to that lift.
Importantly, unless there is malicious intent (thankfully, that’s rare), shock loading is a secondary occurrence that stems from rushing, carelessness and a lack of knowledge. Where I’ve seen shock loading in the past I can usually point immediately to one of those factors and commonly the operator or rigger who has made the error didn’t have the competence to detect the risk before it was too late.
Shock loading accident case study
This is a good example to use because it is based on a hidden element to a lift, which is easy to overlook, yet someone should have fixed it:
A 10t capacity electric overhead travelling (EOT) crane was rigged with a 10t capacity spreader beam. They were being used to lift what was reported to be an 8t box—a fact verified by load cells that had been calibrated and were recording accurate measurements. The box contained a steel component, which formed the majority of its weight despite the fact that it only took up some of the floor space at the bottom of the box. As the load was raised the weight was distributed evenly. No problems so far, but…
The component was supposed to be securely fixed to the bottom of the box but it wasn’t fastened properly and it came loose. As the load became dynamic in the air, the component shifted and was sent hurtling to one end of the box. The rigging at that end of the spreader was catastrophically impacted and the load was left hanging on one end, causing a second shock load and a chain of catastrophe that led to the load falling to the floor.
Other causes of shock loading are numerous and include loads being lifted before slings are tight, jolting of the crane, collisions, breakages, and more.
Actually, the greater acceleration and deceleration of a powered crane is more likely to create a shock loading incident than a manually operated hoist. Of course, care must be taken with all tools, however.
Environmental impact
The environment in which a lift is taking place can increase the chances of a shock loading incident, placing emphasis on the importance of proper lift planning. Industry often considers salt and water corrosion offshore, for example, but dynamic loads imposed on lifting equipment by the movement of vessels and / or sea-state can impact lifting devices used in the maritime sector. Think about a crane lifting a load only for an unexpected movement to create a force in the opposite direction. The lift referenced above could have been replicated offshore, where the consequences could have been even more disastrous.
Of course, all environmental elements and likely scenarios (a rolling sea) should be accounted for in a lift plan and don’t in themselves equate to shock loading but, the point is, in some scenarios the risks are greater.
Aftermath
As always in such incidents the best-case scenario is that only equipment is damaged. In the worst case, someone doesn’t go home that night, or ever again. You can search for videos on YouTube of extreme shock loading events but I’ve seen the consequences myself:
Wire rope jumping off the drum
Top running bridge cranes jumping the rails
Hook blocks damaged beyond repair
Rigging gear destined for the scrap yard
Of course, the impact isn’t always as obvious as the accident above. A shock loading incident might take place but it isn’t necessarily detectable to the untrained eye. As such, operators and riggers continue their operations and put the crane and equipment beneath the hook to work again the next day. They can carry on like this for weeks not knowing that the crane’s gears, hook, bridge, trolley wheels, etc. could all be damaged and on the cusp of breakdown.
Eventually an accident will happen and it might take extensive investigation to trace it back to the shock loading incident.
How to avoid shock loading
There are a number of things you can do to ensure you limit or remove the risks of a shock loading incident. The overarching guidance is to plan thoroughly. That means finding out as much as possible about the load as far in advance as you can:
Are there components within containers that must be secured?
What are the weights involved?
Are centres of gravity offset?
Does the load have pick points?
What rigging configuration will be safest / most efficient?
What rigging gear must be sourced accordingly?
In what environment will the lift take place?
Will the load be able to make a smooth, seamless path to its destination?
Has the rigging gear been inspected?
Do we have calibrated force measurement equipment?
And so on…
In other words, eliminate the chance of a surprise and limit the possibility of a shock (loading).
Working with industry experts, like Ranger, is also a sure-fire way to mitigate risk.