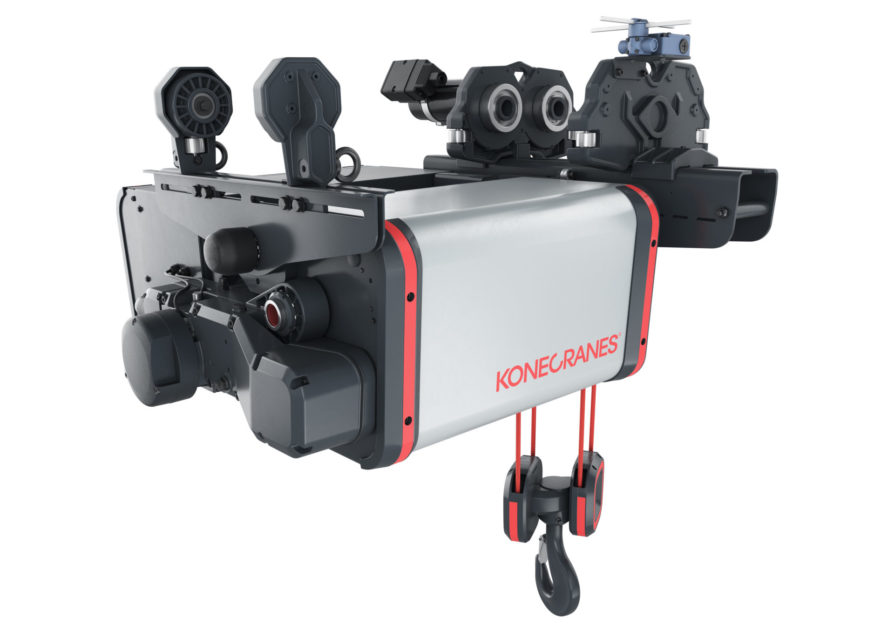)
Synthetic rope benefits powerful hoists
Konecranes has introduced a new synthetic rope upgrade to its S-series hoists, to provide significant advantages over alternative materials.
Synthetic rope reduces wear and tear of both the rope and the components, as it has less surface pressure and friction against the reeving components.
James Dowe, managing director of Konecranes Australia and New Zealand says, “Synthetic rope is also lightweight and safer to handle, because it’s barb free. It requires no lubrication, which reduces maintenance costs over time. Additionally, it is simple to install and can easily bend and guide around the sheaves.
“For companies looking at modernising or updating their existing hoists, synthetic rope is a cost-effective, safe and durable solution, designed to last in service,” he said.
Konecranes S-series hoists are designed to provide more precise and powerful lifting up to 6.3t, with less wear and tear on components.
The hoists set new benchmarks in lifting performance and safety for lift heights up to 24m says Konecranes. Durability and safety are extended with synthetic ropes, and offset reeving provides a 45 percent reduction in overall wheel load.
The Konecranes S-series is ideally suited to a broad range of lifting applications in industries such as manufacturing, materials handling, steel and metalworks and power generation.
“Konecranes has included a number of innovations in these truly forward-looking cranes, including using synthetic rope, tilted drum, offset reeving, and the girder sliding connection,” says Dowe.
The Konecranes S-series features offset reeving, which balances the wheel loads and provides a 45% reduction in overall wheel load due to geometric arrangement of the travelling wheels and reeving system.
The tilted drum radically reduces fleet angles, which eliminates rope crossing and rope peak forces. It also reduces structural twisting, wear, and fatigue with this unique reeving arrangement and robust trolley design.
“Both of these new features were built in to extend crane life, by spreading loads evenly and reducing wear and tear over time,” says Dowe.
Konecranes has revolutionised the main girder of the new S-series cranes, by providing a sliding connection to accommodate bigger tolerances of the crane runway.
The sliding connection also eliminates misalignments and provides easier crane inspections and evaluations because the welds are outside of the main girder, in a specially designed new welded box structure.
To bring further levels of operator control, Konecranes has standardised the inverter for hoisting and taught the crane to understand the hook position.
“Inverter controlled hoisting means more accurate load positioning, safer load handling and less structural demands,” says Dowe.
The new cranes also come with a range of Konecranes Smart Features to control load swing and enhance safety. These include:
- Follow Me – With the Konecranes Follow Me feature, the crane operator can speed up operation by simply guiding the hook, by hand, into position over the load. The crane and trolley automatically follow along, overhead. This feature, which reduces load cycle times by making loading and unloading the crane much easier and faster, is based on continual measurement of the rope angle. To activate, the crane operator turns on Follow Me with the selector switch on the crane’s radio controller.
- Hook Centring – Side pulling puts added stress on ropes and other crane components and sets the stage for hazardous load swing. But the Konecranes Hook Centring feature automatically eliminates side pull of loads and this dangerous scenario, helping to prevent equipment damage and harm to employees. Hook Centring is based on measurement of the rope angle. If the angle exceeds a preset value when the hoist starts to lift a load, Hook Centring activates.
- Snag Prevention – Occasionally, crane hooks, slings and loads accidently snag – or get caught on – a piece of equipment or structural element of a building while in motion. Often this happens before the operator has time to react and prevent damage to the load, the crane or other machinery. The Konecranes Snag Prevention feature automatically stops crane movement in such a situation, when a hook, sling or load accidentally catches on something while the trolley or bridge is in motion. The feature operates on continuous measurement of the rope angle.
All new Konecranes S-series cranes can be fitted with TruConnect Remote Monitoring, which provides real-time information on the crane’s performance.
“This real-time data can be used to make fact-based decisions to improve safety and productivity, as well as optimise planned maintenance schedules to minimise downtime,” says Dowe.
The new S-series is fully backed by Konecranes’ local service network, which includes more than 30 locations across Australia and New Zealand. Additionally, users can easily access all crane information, usage and maintenance data and asset details through the user-friendly yourKONECRANES.com customer portal.
“The customer portal ensures a totally transparent view of the crane’s events and activities, which is an outstanding asset to safety and maintenance managers, and can greatly assist with Standards compliance,” says Dowe.