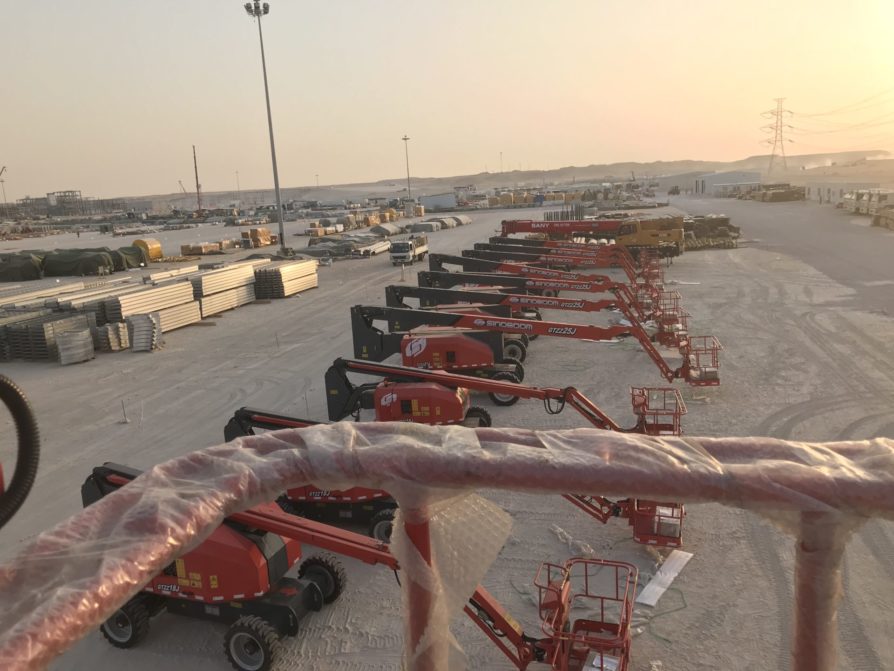)
Raising Our Game
In a turbulent economic environment, productivity gains have never been more important for operators of elevated work platforms. Dan Jenkins highlights some of the ways in which manufacturers continue to raise their game by optimising efficiency for end users.
While there is always more to be done, the productivity benefits of elevating work platforms (EWPs) over scaffold, ladders and towers are widely understood. Time and motion studies have repeatedly and consistently found that EWPs improve efficiency as well as safety when working at height.
Therefore, in recent years, manufacturers have focused on providing additional productivity gains over and above that of existing models. At the same time, they have moved the conversation from comparing EWPs with older methods of working at height, to comparisons between machines.
Raymond Li, Sinoboom’s product manager, says, “This question is one that manufacturers in the access sector need to continue to study and explore. Obviously, numerous engineering applications have demonstrated the value of EWP in comparison to other methods, so there is no doubt that it is a horizontal comparison between products in the EWP sector.”
Platform performance
One area of focus for Sinoboom is boom lift platforms. Li says, “We attach great importance to customer needs and how to help customers improve work efficiency and productivity. For example, the imminent launch of our heavy-duty telescopic boom lift range will allow operators to bring more materials when working at height at one time, thereby reducing the number of lifting round-trips and enhancing productivity.”
This range, launching at Bauma China in November, includes the TB20 Plus, TB22J Plus, TB26 Plus and TB28J Plus, with maximum platform heights of 20m to 28m respectively. For all four models, the platform capacity is increased to 480kg. Sinoboom is expected to release more details on this new series as Bauma China draws closer.
Genie recently announced the global roll-out of its Genie Lift Tools platform, designed for us with the Genie S-65 Xtra Capacity (XC) boom lift. Measuring 4m by 0.91m, it is rated for two occupants and tools, with a safe working load of 270kg.
Amalija Kopac, Genie product manager, Terex AWP, says, “For boom lifts working in constrained work areas, this new extra-large Genie platform enables operators to spend less time manoeuvring the equipment in tight, restricted access spaces. The larger platform also gives operators a more comfortable workspace for long, uninterrupted work.”
Designed for applications such as painting and shipyards, the basket comes with 14 lanyard anchor points, enabling users to take full advantage of the larger platform. It is also fitted with the same digital load sense system as all Genie XC booms. The Genie Lift Tools platform is available factory fitted or as an aftermarket option.
Versatile hybrids
The ability to work indoors and outdoors makes hybrid booms extremely efficient in industrial applications. Earlier this year, Genie launched the hybrid Z-45 FE articulated boom, which it states is designed with productivity in mind. The 16m working height Z-45 FE provides a safe working load of 300kg, with an unrestricted range of motion.
Marie Engstrom, Genie product manager, Terex AWP, said: “With two modes of operation (all-electric or hybrid), the Genie Z-45 FE boom offers rental companies a versatile, sustainable and powerful ‘two in one’ solution adapted to indoor, as well as outdoor, applications; even where on-site electric power is not available.
“And with its robust lift capacity, operators can take up 30% more materials in the platform for increased productivity as compared to other hybrid machines in this height range. These features translate to additional jobsite utilisation and longer rental opportunities.”
Lithium power
Snorkel is bypassing hybrid to focus on electrifying diesel sigma and scissor lifts. This is made possible by lithium-ion batteries, which provide significant productivity benefits over traditional lead batteries.
“As a company we are moving more towards a full electric solution than hybrid,” said Matthew Elvin, CEO of Snorkel. “I am not saying that hybrid is dead, but perhaps, for certain sizes of machine, demand might have peaked. Lithium is the only genuine replacement to the diesel-powered machines that gives you the same duty cycle and work cycle while also being affordable.”
Its first lithium machine was the Speed Level (SL), which will be followed by the S2770RT, S3370RT and S3970RT rough terrain scissors – these went into full production in September 2020. “Very closely behind that will be lithium versions of our narrow compact rough terrains, giving us a complete range of mid-size rough terrain scissors,” added Elvin.
One of the key productivity benefits of lithium batteries is that they do not need to go through a full discharge cycle before being recharged; and they can be rapidly recharged. “With lithium you can quick-charge during the day – you can boost the state of charge back up to 60 or 70% very quickly,” added Elvin. “It is very different to lead acid. For example, in a breakdown or maintenance application, when the workers step off to get parts, they can plug the lithium machine back in and get it back to a healthy state of charge. If you are running 24-hour operations this enables the machine to keep going, which is important in some industrial environments.”
Sinoboom has expanded its lithium-powered range, as well as introducing more hybrids. The company is also exploring how telematics and improve productivity. Li says, “We have always endeavoured to make adjustments and improvements to meet customers’ equipment requirements under differing environmental requirements, for example the introduction of lithium batteries to a number of product lines, and the current application of hybrid power technology.
“Development is an ongoing process, in which we aim to maximise the utilisation rate of customers’ equipment, and improve the customer’s equipment management ability and efficiency, through the application of IoT technology, which helps with fault diagnosis and management in the field, reducing down-time.”
Telematics
The ability of telematics to minimise down time – and enable proactive maintenance rather than reactive repair – has huge potential for productivity.
Niftylift Australia is currently promoting its telematics solution, Niftylink, as a method of both improving productivity and remote working during the ongoing pandemic. “COVID-19 has changed all of our lives at work,” said the company in a statement. “You can keep yourself, your staff and your customers safe and get the most out of your machines with Niftylink. As business re-opens, we all need to find new ways to manage and maintain machines with new social distancing rules and safety measures in place.
“The new Niftylink system offers a useful solution to this challenge and it can be retrofitted to all Niftys. Niftylink is proving a powerful tool for all Nifty owners. We all need a smarter more efficient approach to managing our fleets, processes and services so that we can continue to trade successfully. But we also need to stick to the new safety measures being introduced due to COVID-19. Niftylink, our powerful telematics tool, allows rental company owners, fleet managers and service technicians to do just that.”
Skyjack has added a new battery management system (BMS) to its Elevate telematics platform, which is providing some surprising insights into battery life. This has huge potential for productivity, as battery issues are one of the main causes of down time and service engineer call-outs.
Malcolm Early, Vice President of Marketing at Skyjack, said: “We identified that batteries are currently sitting at an average battery life that is only half their potential. Getting these insights into the hands of all industry roles is critical to meeting that potential.”
Through a data sharing collaboration with key customers, Skyjack was able to analyse battery charging and state of charge which feed into how Elevate BMS works. For example, the study showed that batteries typically only received one full charge a month, with three quarters of battery charges lasting less than 2.75 hours. This lack of understanding of how to keep the batteries in good condition can be addressed at end user level by a good BMS solution.
David Swan, technology product manager at Skyjack, says, “Looking at the results from the study it’s clear that there is a lot of opportunity for better practices and greater profitability with rental companies current stock of lead-acid batteries.
“A lot of that opportunity is at the operator level and that’s why we incorporated ELEVATE BMS into our new ELEVATE Live product where the emphasis is on changing charging behaviour through active on screen prompts directed toward the operator.”
Electric scissors
Skyjack is introducing a range of improvements to its slab scissors, including its Eoctray leak containment system for DC electric scissor lifts. Ecotray prevents any potential leaks from hydraulic systems dripping onto floors or other internal components of the scissor. It aims to replace what the industry commonly calls “diapers” for absorbing leaked fluids. This is of particular benefit for applications on expensive flooring, in clean rooms and other areas where hygiene or chemical contamination are of concern.
Kris Schmidt, product manager at Skyjack, says, “The idea of the so-called diaper has been around for some time. However, they have proven cumbersome to employ and restrict key lift functionality, so we looked at something different. Unlike other systems that focus on the main hydraulic tray, ECOTRAY also protects against leaks from drive motors and steering cylinders.”
Available as a factory install or aftermarket option, Ecotray uses a series of catchment trays that contain absorbent pads, which can be quickly and easily replaced. As a field kit, it can be fitted in 10 minutes and has been designed to be installed without the need for tools. The changing of absorbent pads takes seconds and replacements are available directly from Skyjack parts.
Meanwhile, Genie is approaching slab scissor productivity from a different angle, by switching from DC to AC to direct drive.
Chad Hislop, senior director of product management at Genie, says, “AC direct drive is a super-efficient drive system for electric scissors. You benefit from longer-lasting batteries and significant savings over the life of the machine, at a very small price increase for the customer. A scissor which costs you far less in batteries and far less to maintain is a great proposition.”
Genie is phasing in AC direct drive for all its slab scissors over the remainder of 2020. The direct drive version of the GS-4655, the largest slab scissor in Genie’s range, is now in full production. “My prediction is that, as customers get their hands on the E-drive scissors, they will switch their buying preferences pretty quickly,” said Hislop. “There really are no negatives to E-drive systems compared to hydraulic systems, so we expect really quick adoption.
“I think it is a no-brainer. A lot of customers already know the savings available, they just needed someone to come out with a machine that is produced correctly. They already have experience of AC drive motors through the Z-40 narrow boom, the 69 DC scissors and the Z-60 FE. People are so comfortable with the technology that they are asking us for it on slab scissors. Everyone wants AC drive right now.”
Fit for purpose
There remain some areas where EWPs are still in the process of replacing traditional methods such as scaffold or podium towers – for example, spider lifts and low-level access platforms. However, increasingly, optimising productivity is about selecting the right machine for each task. For manufacturers, this means ensuring they provide a diverse product portfolio.
“Of course, with the continuous application and promotion of the EWP as a working-at-height solution, more and more industries are aware of its safety, efficiency, and convenience,” says Sinoboom’s Li. “Therefore, corresponding research is also being carried out in non-construction fields, such as petrochemical and shipbuilding industries, and Sinoboom products are in regular use by customers in these industry sectors.
“Our machines have been specifically tailored to withstand the uniquely harsh environmental pressures of these industries, with enhanced dust- and corrosion-proofing, durable paintwork and optimised stability to withstand windy conditions. All these measures enhance productivity by reducing machine downtime.”